8 things to know on metal insert injection molding: our experience and know-how at the disposal of your project
21 November 2023
Metal insert injection molding has gained popularity in recent years as a cost-effective and efficient manufacturing process. This technique uses plastic molds to create products incorporating metal components, offering various advantages such as costs reduction and faster production times. In this article, we will describe the fundamentals of metal insert injection molding and explore its potential benefits for your business.
Metal insert co-molding involves fixing a metal insert in the mold before injecting plastic. Despite its simplicity, there are important considerations for successful implementation:
- Shape and Dimensional Accuracy- Uneven shrinkage points can affect the dimensional shape and accuracy of the mould. Therefore, testing is essential before the injection molding process.
- Deformation and Shift - Metal inserts can deform or shift during injection, requiring careful consideration of mold structure and design to securely retain the metal insert.
- Experimental Preparation - Products with rigid metal insert shapes require thorough experimental preparation to address potential challenges in the molding process.
- Mold Structure Constraints - In order to improve the overall process, it is important to predict the constraints of the mould structure, including the positioning of the door and the moulding cycle.
- Preheating or Drying - Determine whether the metal insert needs preheating or drying to ensure product quality and molding stability.
- Factors Affecting Molding - Various factors, including the accuracy and shape of the metal insert, mold design, and product shape, influence molding rate, productivity, and production costs.
- Effective Combination of Equipment - Maximising the performance of an automatic insert moulding system is achieved through an effective combination of injection moulding machines and moulds.
- Cleaning and Maintenance of the mould
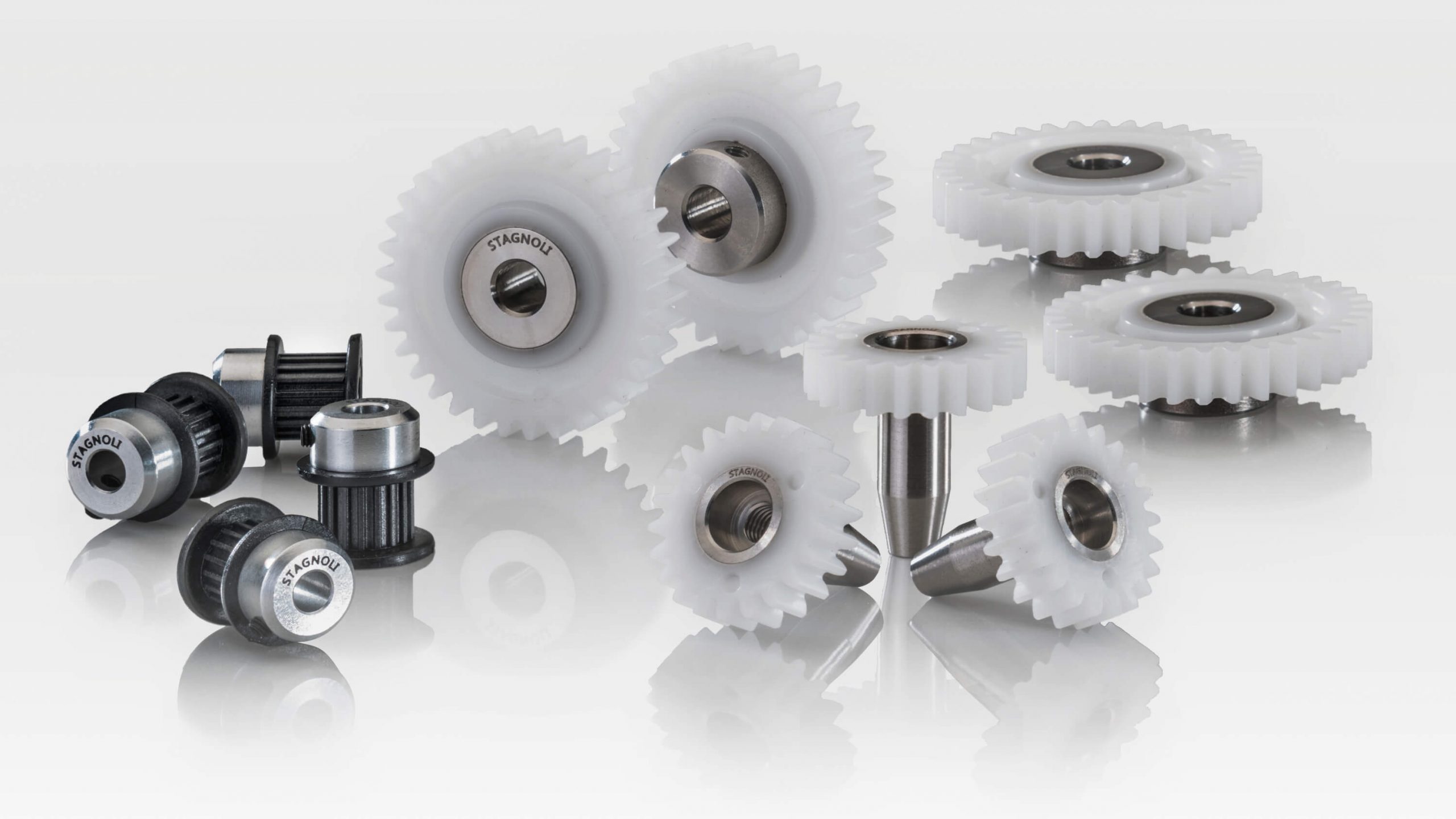
Production process operation
The moulding of metal inserts involves several production steps:
- Preliminary preparation of the metal inserts and subsequent filling of the mould.
- Injection of the plastic material melted with the inserts applied to create an integral product.
Out-sert moulding
Out-sert moulding is a similar method to the traditional injection moulding process. The main difference is that out-sert moulding takes place on the local surface of a sheet metal.
The goal of both methods is to achieve flexibility in applications and product design.
The metal inserts used in this process include:
- Metal shaft (steel, aluminium, etc)
- Metal Hubs
- Bearings (used for idler gears or plastic planetary gears)
- Steel Bars (used for linear elements, such as racks)
- Magnets (used for electric motors, automotive applications, or limit switches).
- Sensor gears, which are used to monitor the angular position and/or speed of a gear in critical applications.
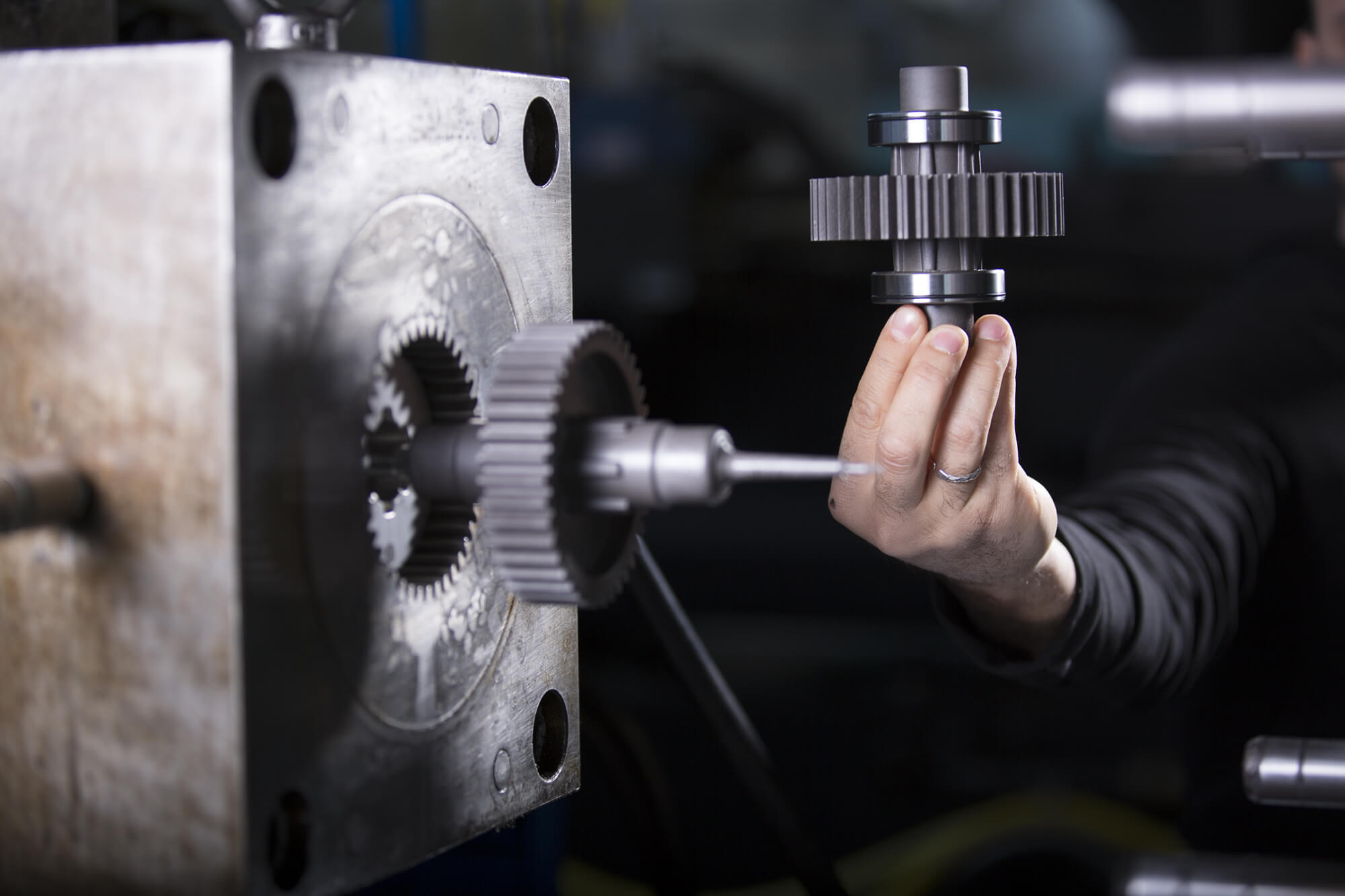
Features and advantages of over-molded gears and power transmission
- Increase in the precision of shaft and gear coupling.
- Increase in the mechanical strength and torque transmission of the plastic Gear or Pulley.
- Possibility of avoiding subsequent assembly between metal and plastic by having the finished part during the molding cycle.
- Advantages of the combination of metal and plastic components (self-lubrication, quietness, lightness).
- Reduction of vibrations and noise: plastic gears are much more effective than their metal counterparts in limiting shocks and vibrations. In fact, plastic gears, unlike metal ones, are not subject to the same shaking or trembling.
Overmoulded metal gears and power transmission
Thanks to our experience in the plastic moulding sector, our continuous investment in R&D, and our know-how, we are the benchmark in the field of design and production of overmoulded gears.
In addition, we have optimised the production process thanks to our expertise in the overmoulding of:
- Single and multi-cavity magnets for the automotive and household appliance industries.
- Steel shafts with plastic helical gears for the automotive industry, in particular for windscreen wiper motors.
- Metal inserts for the e-bike and e-mobility industry with and without a key.
- Bearings for planetary gearboxes, chain tensioner pinions and idler gears.
- Steel bars for precision racks and plastic linear elements.
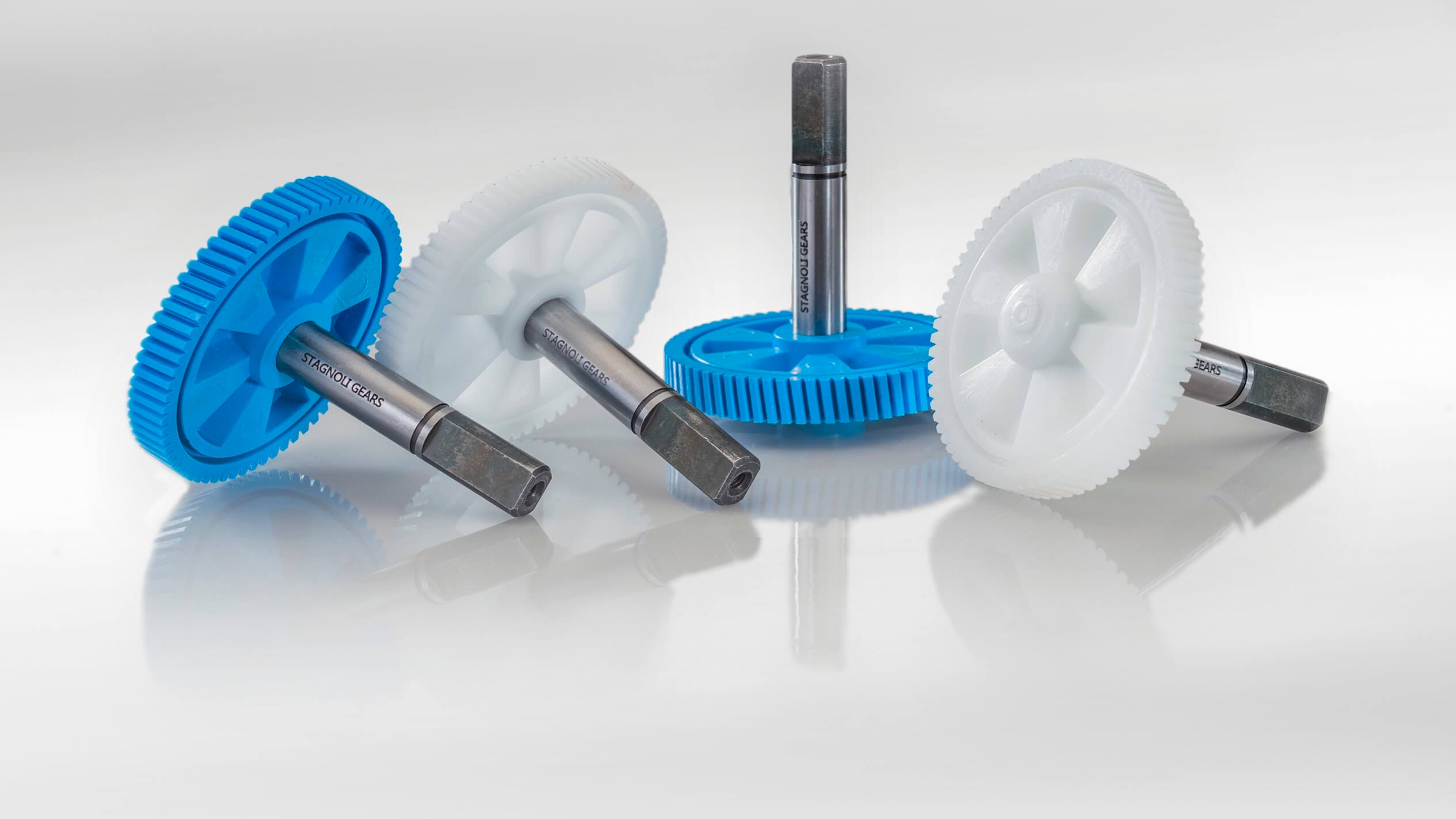
All these applications have been developed internally with different plastics material such as PA46, POM, DELRIN, and PPA.
Technologies for Molding Gears with metal inserts and Bearings
- ARBURG vertical molding machine for co-moulding metal inserts with rotary table.
- Automatic moulding of inserts by robots. The aim is to ensure that the technical and quality requirements of the customer are met.
- Manual and automatic inserts and magnets’ pressing on full electric presses with vacuum technology.
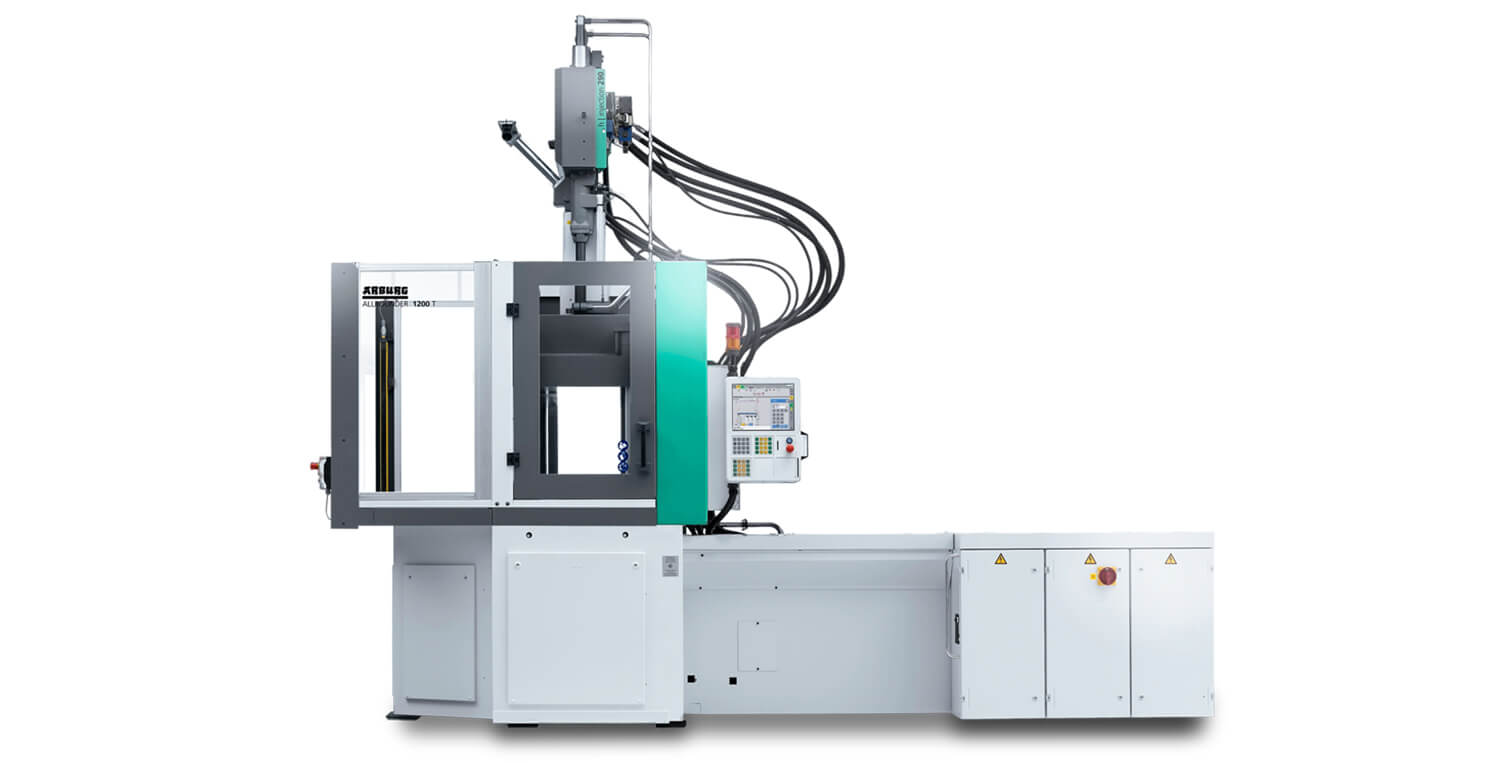
Contact Stagnoli Gears today for your next project requiring overmolding.